Jonathan Seddon: The future is pre-fab
Morton Fraser’s Jonathan Seddon determines the pros and cons of a modular approach to delivering homes compared to traditional building.
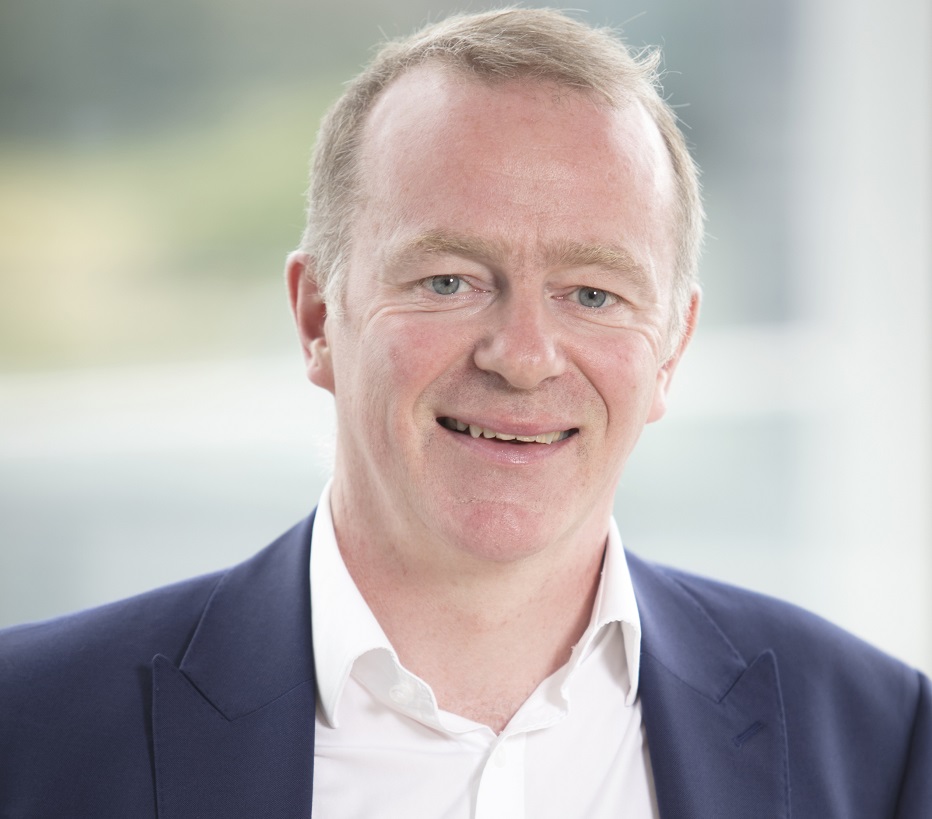
Jonathan Seddon
The use of the pre-fab (or modular) building is by no means a new concept in the UK. Historically, it came to the forefront of construction following the Second World War. At a time when there was a large demand for housing stock, pre-fabricated buildings provided a solution in delivering housing quickly and at lower costs. Fast forward 70 or so years and we find ourselves in the midst of another housing crisis. Could pre-fab buildings be the answer again”
The concept has undergone something of a revival in recent years and looks to have an important role to play in the future. The UK has been generally slower to respond compared to other countries who have shown innovation in design and construction methods resulting in the increase of pre-fab buildings in cities across the world. In particular, Scandinavian countries are leading the way in this area.
One of the biggest hurdles to the growth of pre-fab buildings in the UK is the association with post-war construction. Many view such buildings as dull and unappealing, certainly not what people imagine as their dream first home or a trendy place to work. It is clear that some form of persuasion is required to turn peoples’ minds.
The factors pushing the revival of modular construction
It reduces time. Modular construction is carried out off-site. It is then transported in segments and assembled together on site. The construction takes place in factories set to controlled conditions. This avoids the natural elements of working outdoors and subsequent weather delays caused by a harsh winter. It also improves the working conditions for workers with factories generally being safer places to build, reducing delays and allowing for more efficient construction.
It reduces disruption to local residents and businesses. A large development, whether residential or commercial, results in the arrival of a number of lorries with deliveries, cranes and other substantial machinery together with an influx of workers and general increase of noise to the location. With pre-fab the work required on the site becomes much more streamlined and results in less time and disruption to the local area. One drawback to this is that the buildings have to be transported to site. This may cause logistical issues and limitations as to what may be capable of being transported, especially in large built-up areas.
There is less of an impact on the environment. At a time when climate change is at the forefront of policy-making, modular construction may lead the way for a more “environmentally friendly” form of building. Due to the shorter construction time, the carbon emissions will inevitably be lower. Some research carried out suggests the reduction in carbon footprint of off-site building may be as much as 40%. There is likely to be a reduction in wasted materials too. With construction taking place within factory conditions, materials are less likely to go to waste. Further, modular buildings can be taken apart and recycled, without the need for demolition and, as with traditional buildings, turning to rubble and waste. With developers and construction firms likely to come under increasing pressure to improve their environmental impact and sustainability, pre-fab building may provide an effective response.
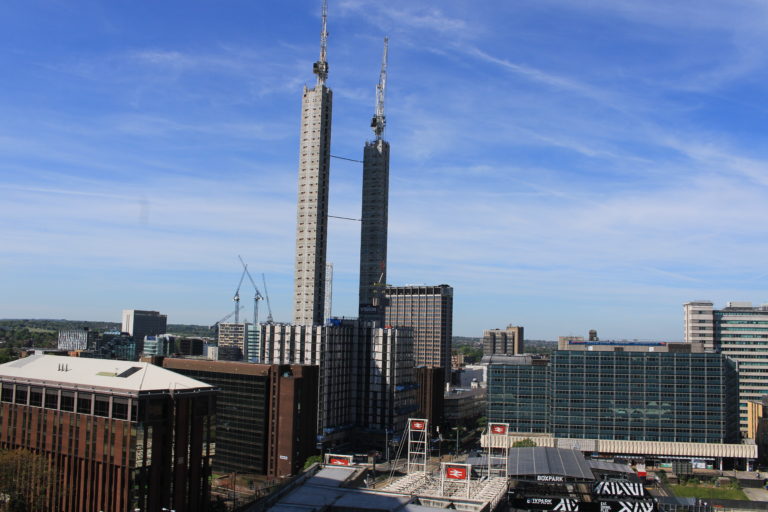
The world’s largest towers built using modular construction are nearing completion in Croydon
Hurdles to building becoming mainstream in the UK
Heavy investment upfront is required. As explained above, the work still has to take place somewhere and this is usually in large specialist factories. These sites are not cheap to operate from. A reasonable estimate may be up to £100 million to construct and fit-out with the necessary machinery and equipment. These costs would generally be passed on to end-users. In the current economic uncertainty, one may ask if there are organisations who would be prepared to make such an investment when they may not reap the returns for some years.
Obtaining finance is likely to be more challenging. As an emerging market it is not one traditional lenders are familiar with and it is not surprising that they will take a more cautious approach. Although land is acquired in the usual manner, the fact that construction takes place off-site presents a higher risk to lenders as funds would require to be forwarded to contractors for materials off-site raising questions as to risk and legal title. Lenders usually have the protection of securities over the land but with modular construction, they are relying on moveable property in the hands of contractors, a riskier position for any lender. In other words, a building not in its final location will not be viewed as a profitable venture to most commercial lenders. Careful consideration will be required in the legal drafting for such projects to protect both the lender and borrower’s position.
The mortgage market is also likely to be a cautious player having little experience in this type of housing. A lender requires a property to be eligible for a mortgage and have a marketable title. Until the building is in the ground a lender may be unwilling to grant a mortgage or if they do, it may incur higher costs for the borrower. This will be an interesting area to watch in terms of how it develops in the event that modular housing developments become more prominent. At Morton Fraser we have acted for a bank in the development funding of a couple of pre-fabricated buildings recently. Whilst not standard, these structures are perfectly fundable if set up properly.
Mindsets and attitudes to prefab buildings
Particularly in Scottish city centres where traditional buildings are prominent, this is what people are accustomed to. They may question the quality of modular buildings being transported to a site. Such attitudes will inevitably lead to a knock-on effect on selling on values. This is likely to be the greatest challenge and perhaps a form of trendsetting is required to turn peoples’ attitudes to the feasibility and attractiveness of such buildings. At a time when many areas are undergoing renovation projects, it is interesting to see if pre-fab buildings play an increasing role.
It is possible that modular buildings will become a blueprint for future development in both the residential and commercial markets. Its flexibility means buildings can serve many sectors including retail, industrial and residential. Time will tell whether such buildings will hold up to traditional methods but with increasing environmental concerns and the cost pressures on developers, pre-fab buildings certainly appear to provide some answers to these challenges. However, most importantly, attitudes, whether rightly or wrongly, will have to change.
- Jonathan Seddon is a partner and head of construction law at independent law firm Morton Fraser