And finally… Low carbon reinforced concrete trialled
An industry-first low carbon reinforced concrete solution is being trialled on National Highways M42 Junction 6 improvement scheme.
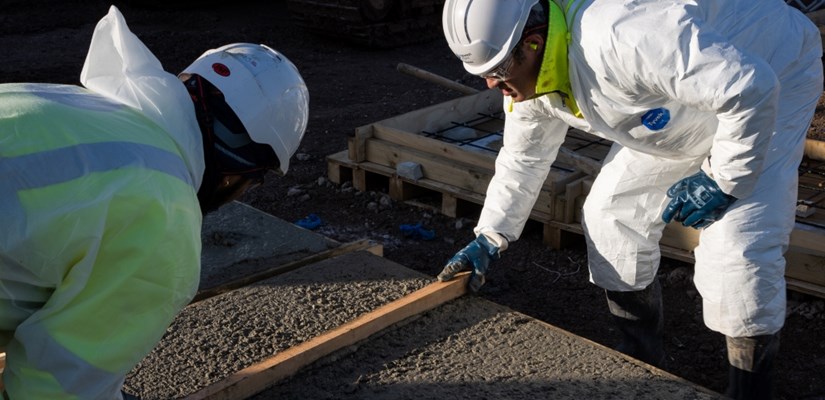
The £282 million project – designed to alleviate congestion for motorists at a well-known bottleneck in the Midlands – is trialling the use of low carbon concrete and basalt fibre reinforcement on a temporary haul road for construction vehicles.
The trial, led by Skanska, in partnership with the National Composites Centre and funded by National Highways (NH), compares traditional steel reinforced concrete with a low carbon concrete reinforced with basalt fibre.
Production of cement, a key ingredient in concrete, currently accounts for around seven per cent of the world’s CO2 emissions. In the UK, this figure is less than 1.5 per cent thanks to the industry’s innovation and investment in efficient plant, fuel switching and the use of low-carbon cement substitutes that are by-products from other industries.
Tarmac, a member of the project’s supply chain, provided two types of concrete for the trial: a mix comprising conventional blended cementitious material and a low carbon alternative mix incorporating an Alkali Activated Cementitious Material (AACM) in place of the cement.
Robert Gossling, head of commercial engineering for Tarmac, said: “Tarmac has developed new low carbon concrete technology and this trial is a great opportunity to collaborate with industry leading project partners to test its performance through an ideal, real-life application.
“Manufactured at a conventional concrete plant located close to the project and installed in exactly the same way as traditional materials, this new sustainable product delivers a carbon footprint up to 80 per cent lower than a standard CEM I concrete. We hope this demonstration will help to accelerate the development of innovative low carbon materials.”
Malcolm Newton, director at Basalt Technologies explains why their basalt fibre reinforcement is being trialled as an alternative to steel: “Basalt is a lightweight composite material consuming 62 per cent less CO2e than steel during its manufacture. It comprises a non-metallic inert material that does not corrode, making it more durable than steel. Basalt Fibre reinforcement is also 4 to 5 times lighter than steel, making it safer to handle, fix and transport with fewer lorry movements.”
Glennan Blackmore, operations director (Highways), Skanska UK, said: “With support and funding from customer National Highways, we have been able to bring together the knowledge, skills and innovative thinking from expert teams within Skanska, the National Composites Centre and supply chain partners Basalt Technologies and Tarmac to carry out this exciting trial.
“Through using a unique combination of materials, we are working to not only cut carbon, but also aiming to improve the structural performance of reinforced concrete and deliver better productivity, safety and cost outcomes.
“It’s a great example of how by working collaboratively we can innovate to help tackle climate change, by working towards net-zero carbon solutions, and deliver long-term benefits for the industry.
“We are thrilled at the progress achieved to date and we are very excited to see the results.
“The combination of the low carbon concrete and the replacement of the steel with a lightweight composite reinforcement dramatically reduces the carbon footprint by more than 50%.”