And finally… Robotic dog to capture data on construction sites
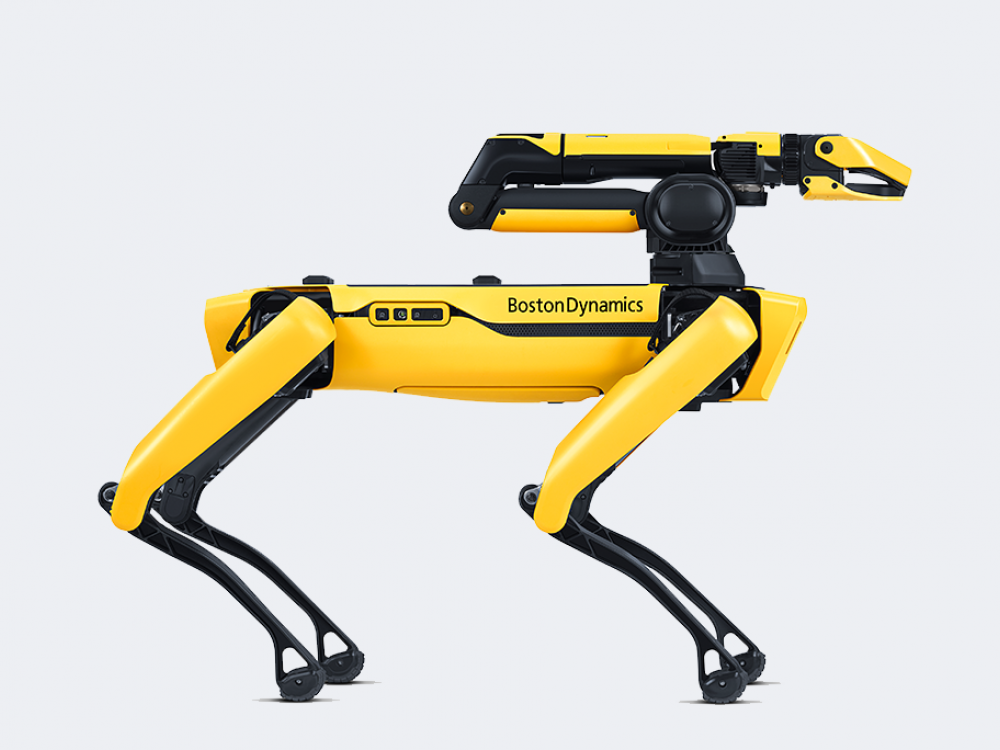
New 3D laser scanner technology and software from Trimble have been integrated with Boston Dynamics’ ‘Spot’ robot to produce a fully automated robotic scanning solution for construction sites.
Trimble said its exclusive turnkey solution facilitates autonomous operation on construction sites and takes advantage of the robot’s unique capabilities to navigate challenging, dynamic and potentially unsafe environments. Trimble’s 3D data capture technology, integrated with Spot, enables a continuous flow of information between the field and the office for consistent, ongoing documentation of job site progress.
“The relationship between Trimble and Boston Dynamics is really special. Users don’t have to figure out the integration of the scanner. It also enables us to work with only one vendor,” said Thai Nguyen, director of Virtual Design and Construction, Hensel Phelps. “Using the X7 integrated with Spot lets us document changes on the jobsite and make important decisions in the field, rather than waiting hours or potentially days for the information to be relayed to our project staff. This allows us to make the best decisions as quickly as possible with the best information.”
“Our construction customers require turnkey solutions for autonomous jobsite documentation and analysis. Boston Dynamics’ strategic alliance with Trimble has allowed us to build that solution collaboratively by combining our strengths in robotics and construction, respectively,” said Brian Ringley, construction product manager at Boston Dynamics. “This unique integration is simply unprecedented—it’s never been easier to scan a jobsite, and the increased scanning frequency is creating new opportunities in automated project analysis and insight.”
The integration is focused on the automated capture of field construction data through the use of Trimble 3D capture technology and the Spot robot. The autonomous workflow for the X7 laser scanner uses fully integrated Spot robot controls in FieldLink software to create a predefined path of waypoints for Spot to follow and collect laser scans. The data collection missions can be scheduled to run on a regular and consistent basis for design validation and progress reporting. The advantage of this combination is increased efficiency and real-time, as-built data analysis in the field and in the office.
Laser scans collected using the X7 scanner and the Spot robot can be tied to a jobsite project coordinate system, as well as individual scan stations. The data is collected, and then made into a composite point cloud in real-time on the Trimble tablet controller before leaving the site. While performing autonomous operations, Spot’s docking station enables the in-field charging of batteries on both the robot and the X7 3D laser scanner, and also provides the continuous transfer of data through a Gigabit Ethernet connection to the office.