And finally… Underground robot to revolutionise pipe inspection work
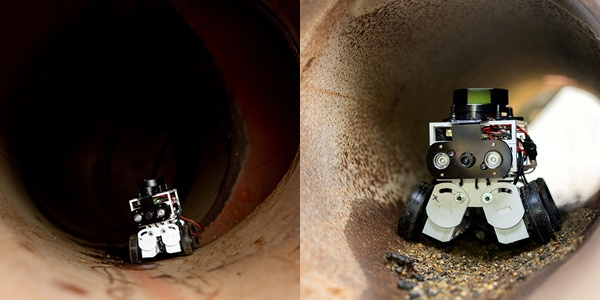
Ratty the Robot
Robotics experts at the Manufacturing Technology Centre have developed an autonomous robotic rat which can scurry along underground pipes carrying out inspection work.
The invention has the potential for cost and efficiency savings for utility companies as well as reducing human exposure to hazardous environments and preventing pipework leaks.
‘Ratty the Robot’ is a tetherless wheeled inspection robot with a laser-based navigation module, with the potential to carry out tasks in environments which would defeat most robots.
The robot’s ability to access and work autonomously in difficult conditions has the potential for major costs savings for utility companies as well as removing risks associated with working in hazardous environments. As the robot can self-drive it reduces the need for a human operator. It has the added advantage of automatically mapping complex pipework and tunnel systems which have built up over many years.
MTC advanced robotics research engineer Dr Mahesh Dissanayake said the pipe-crawling robot could give the utilities sector opportunities for cost saving combined with increased efficiency, and demonstrated how robotics and automation can benefit a wide variety of sectors.
Dr Mahesh Dissanayake said: “This proof-of-concept robot can travel in confined spaces, inspecting networks while working fully autonomously. It opens up the opportunity of inspecting far more of the underground network at a much reduced cost, reducing failure rates and flagging up potential problems. With technology advancing all the time the next exciting step could be a robot which not only inspects pipework, but is capable of carrying out repairs remotely without having to dig up roads.
“This project demonstrates the MTC’s determination to support the utilities industry by providing solutions that can reduce downtime, cost and risk. The transferable technical know-how will also allow the MTC to support the automation of other activities in hazardous or difficult environments.”
Currently, most advanced inspection work of drainage, sewage and gas supply pipes is carried out by tethered devices managed by operators, which is costly, slow and labour intensive, with difficult to reach areas. The MTC’s concept robot is tetherless, with the ability to operate autonomously and navigate confined areas, enabling the operator to focus on the inspection.
The robot has successfully undergone simulated trials at the Synthotech test facility in Yorkshire.
Simon Langdale, engineering director at Synthotech, said: “It’s been great to put this proof of concept though its paces in a range of simulated environments. Automation of inspections for pipes is a key area that can help build better understanding of the complex infrastructure underground. We have been able to benchmark our current live access robotics against automated robotics and make sure that we can stay at the cutting edge with support from the MTC.”
The MTC aims to provide a competitive environment to bridge the gap between university-based research and the development of innovative manufacturing solutions, in line with the Government’s manufacturing strategy. The MTC is part of the High Value Manufacturing Catapult, supported by Innovate UK.