Blog: Managing risk throughout the construction materials shortage
Eilidh Dobson
Eilidh Dobson and Iain Drummond comment on legal aspects of the ongoing materials shortage.
It will be news to few that the construction industry is experiencing a serious shortage of key materials. The Construction Leadership Council first warned of shortages (in timber, steel, pitched roofing, plastics, paints/coatings, some electronic components and cement – among other materials) early this year, and has reiterated its concerns since. Those concerns are so severe that rationing has been proposed as a potential solution – although, to date, this approach has not been adopted on a wide scale in the UK.
The causes of the shortages, too, are well known: exceptionally high demand globally, supply issues linked to Brexit and difficulties arising from Coronavirus have all had an effect. A global shortage of shipping containers is another factor.
The result is low availability of materials, and high prices. The effects are being felt across the industry – with smaller contractors thought to be suffering especially.
With the shortages expected to go on for some time, many in the construction industry will be considering what exposure they have to additional costs or claims. A cautionary example is that of South Ayrshire Council: it was reported last week that the cost of constructing a planned new school has risen from £52.86 million to £59.33 million, as a result of materials shortages. The increased borrowing is expected to cost the council an additional £400,000 per year.
What issues might arise?
When faced with a difficulty obtaining materials, there are generally three options: first, the contractor purchases available materials at an unexpectedly high price; second, the contractor purchases alternative materials; and third, the works are re-programmed or delayed until materials are readily available.
Unsurprisingly, which party bears any additional cost will depend on the precise wording of the relevant contracts.
The cost of materials: who pays?
Where the cost of materials has been factored into the prices agreed at the time of contracting, there may be limited or no opportunity for the contractor to have these prices amended. Parties should consider carefully the particular terms of their contract, and be alive to opportunities to limit the impact of any unhelpful rates (e.g. when negotiating any changes or additional works).
One way in which risk may be balanced between employer and contractor is if contractual provision is included for price adjustment based on inflation. An example of such provision is in the NEC4 Conditions, Secondary Option X1, which provides for index-linked price adjustment. The obvious downside to an employer is the inherent lack of price certainty; however, this may be palatable where the alternative is to accept a tender price based on ‘worst case scenario’ materials costs.
An option to limit exposure to rising and uncertain prices may be to purchase materials in advance (if materials are available in advance, and can be stored). An employer considering funding such a purchase may wish to require provision of an advance purchase bond (in terms of which sums would be payable to the employer should the contractor fail to procure the relevant materials).
Are alternative materials an option?
An alternative material may be more readily available. Whether or not a contractor is permitted to make such a change will depend on the agreed specification, and – of course – the full contractual terms.
Often, material changes to the specification will only be permitted with agreement of the employer. Where the choice is between using the alternative material and considerable delay to the project, a change may be the most attractive option to all parties. Early communication between parties will be helpful.
Delay, suspension and re-programming the works
Where materials cannot be sourced, there may be no option (or, at least, no reasonably practicable option) but to delay – or even suspend – the works. In that scenario, who bears the risk?
Most construction contracts provide particular circumstances in which the contractor is entitled to claim additional time and costs in the event of delay. Negotiating parties may wish to consider standalone clauses to cover scenarios linked to materials shortages - for example, apportioning risk in the event of a delay at port. Such clauses must be carefully considered so that their scope is only as wide as the parties intend.
Similarly, most construction contracts contain provisions setting out when – and at whose cost – works can be suspended. Particular care to comply with relevant contractual requirements should be taken by a contractor considering suspension, as ‘downing tools’ without due cause may open the door to early termination.
Parties should also consider what provision their contract makes in the event of a change in law, which may be relevant if – for example – coronavirus regulations have delayed or prevented delivery of materials. Contractors will often be entitled to additional time and money in the event of such a delay – provided that the change in law can be proven to be the cause. This may be difficult where there have been several contributing causes, and/or where limited evidence exists of the immediate cause of the issue.
Whether a claim is for time and costs arising from delay, suspension or a change of law, the success of that claim is likely to depend on more than just meeting the relevant contractual test. The party asserting entitlement generally must also be able to prove what additional costs it has incurred, and must comply with all contractual requirements for bringing a claim (which may include a strict notification requirement).
In all cases, where progress of works is at risk, consideration should be given to whether remaining works can be reprogrammed to reduce delay. Failure to do so may be criticised as a failure to mitigate loss, which is likely to impact on the costs recoverable by the contractor.
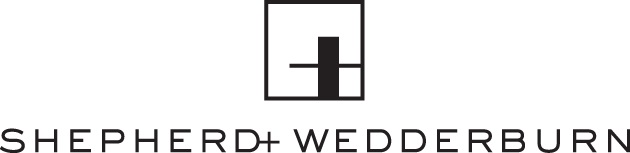
Eilidh Dobson and Iain Drummond are lawyers at Shepherd and Wedderburn