Derek Lennon: Investment in new onsite techniques can help accelerate housebuilding
Sheet piling quick hitch Thornliebank
Derek Lennon from Akela Construction & Ground Engineering looks at the innovative techniques the firm is employing to help tackle the growing housing shortage.
There is no silver bullet to the UK’s chronic housing shortage. Compounded by the Covid-19 pandemic, it’s an issue with far-reaching consequences. Despite the supply chain now bearing the brunt, coupled with labour shortages and skills gaps across the workforce, the need for housing continues to increase with demand outstripping supply.
Debate over the barriers to meeting house building targets is complex. Not all of these are easy to resolve but increased investment and advances in the equipment can play a part and offer solutions.
For housebuilders there is a real opportunity to harness new techniques on offer from ground engineering firms to allow for efficiencies and help tackle the housing deficit.
A Pagani CPT Rig in Tranent
When ways of working have been largely the same for decades it can be daunting, not to mention logistically difficult and expensive, to change. Sometimes it takes one or two developers to take a leap of faith and embrace new processes, delivered by experienced contractors, for others to follow suit.
In recent years, Akela Group has taken decisions to invest and roll out new techniques to our clients. Not only are these simple and easy to utilise, they are now resulting in significant time and cost savings – allowing for faster and more efficient house building. It’s encouraging to see housebuilders adopt new ways of working which are enabling them to get on with the job faster.
One area where we are seeing the biggest positive impact is site investigation which can be a time-consuming task for any builder as they determine layouts for developments. As ground conditions differ over short distances, accurate data and suitable area coverage is critical when assessing the suitability of a site.
A vibroflot on quick hitch at Avant Stewarton
Investment in innovative techniques, like Static Cone Investigation for example, can revolutionise the way in which developers can test the strength and suitability of soil. Traditionally seen as bespoke and specialised, Static Cone Investigation is becoming more mainstream with Cala, Bellway and Avant all using it on their sites, saving weeks worth of time and eliminating the need for time-consuming piling work.
The quality of the data and information produced by the static cone enables housebuilders to get onto a site quicker with no surprises. There is now real potential for this to be used more widely at an earlier stage in a project timeline.
Doing significant site work within close proximity of other buildings and occupied homes can present multiple challenges, particularly vibration and noise. Minimising these risks can, in most cases, result in work continuing without delay. Whether using an excavator mounted torque driver and pre-bore auger to manage vibration risk or installing screw piles to overcome ground obstructions, developers choosing these more advanced technologies are seeing their output increase.
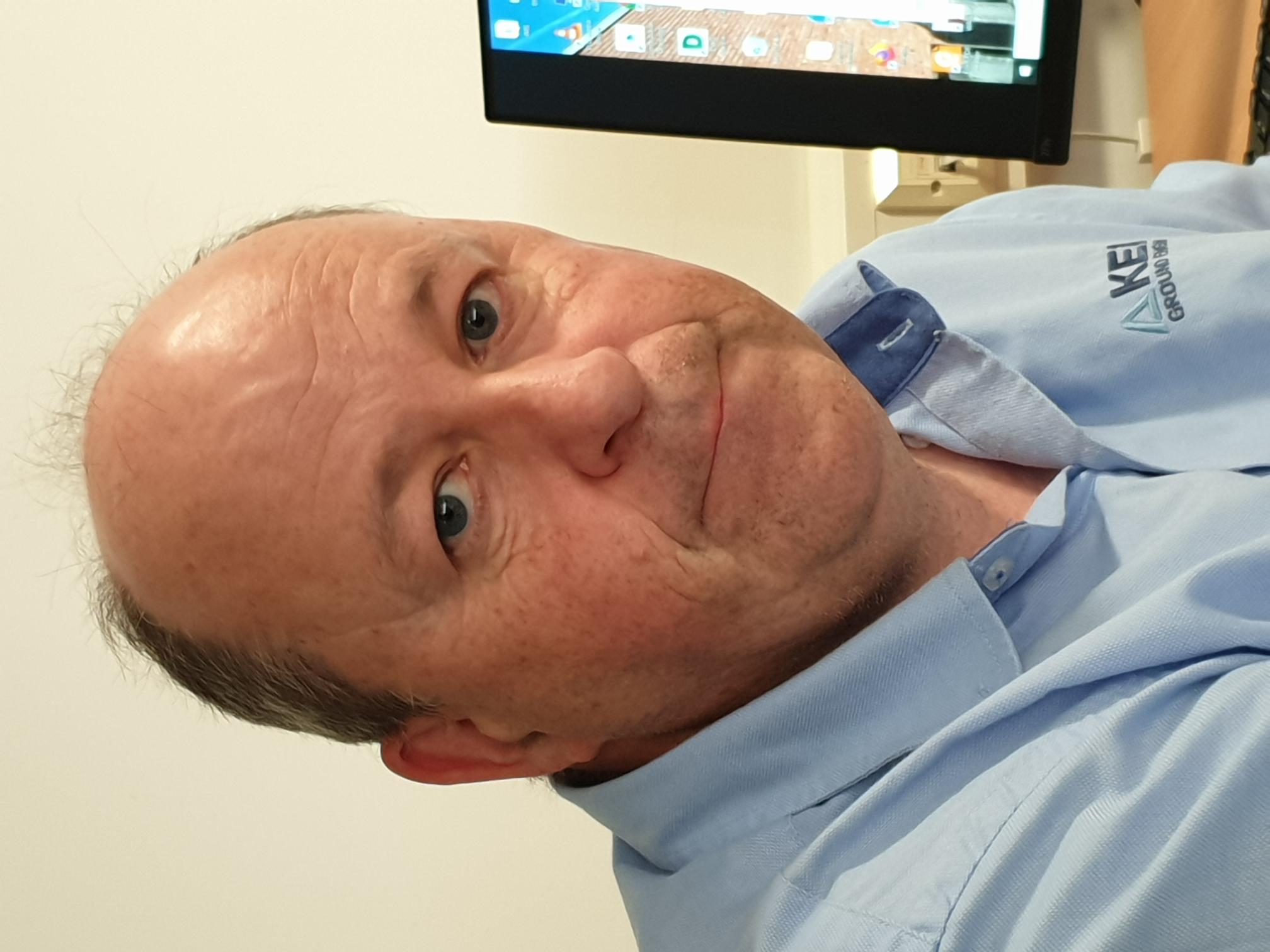
Derek Lennon
Prefabrication of materials off-site is also an increasingly cost-effective and viable option for developers who simply need to take delivery and install. Akela, for example, is the first company in Scotland to produce high quality reinforcement jointing systems and cages of various sizes. This process is two to three times faster and offers significant cost savings as there is no site steel fixing required.
Running in tandem with advances in technology, sustainability will continue to be a crucial factor as we work towards delivering housing targets. Minimising our carbon footprint while improving onsite efficiency will be a tricky balancing act but one which we all must embrace. One such process we have been focusing on at Akela is minimising soil waste using a 2.5 tonne excavator-mounted soil mixing bin. This can help improve surface condition and recycle existing soil which we do by mixing lyme into the aggregate to enhance quality. This, in turn, reduces the requirement for thousands of tonnes of soil to be transported around the country - therefore cutting fuel emissions of our vehicle fleet.
Times are changing and with this comes new ways of working – many of which are resulting in demonstrable benefits for housebuilders. Let’s grab these opportunities with both hands as an industry collective and help meet the demand for safe, affordable and quality homes.
- Derek Lennon is geotechnical design manager for Akela Construction and Ground Engineering Ltd