Embodied carbon regulation ‘urgently required’, say industry professionals
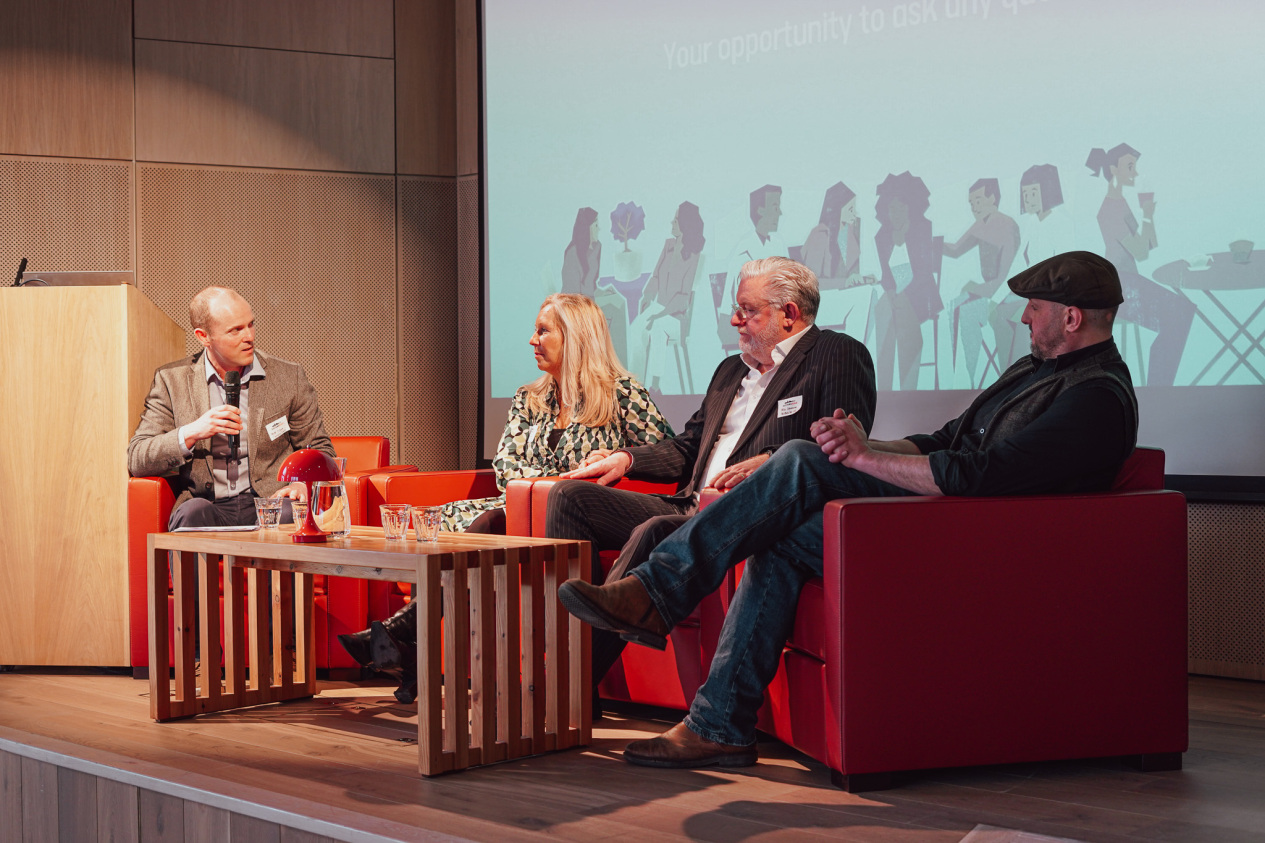
Regulation of ‘embodied carbon’ is urgently required to accelerate the decarbonisation of the built environment, according to industry professionals who gathered to discuss the role that building materials play in the country’s journey to net zero.
Embodied carbon is the term to describe greenhouse gas emissions arising from the manufacturing, transportation, installation, maintenance, and disposal of building materials.
The issue was discussed at a recent Sustainabuild Scotland event in Edinburgh where industry professionals gathered to discuss the role that building materials play in the country’s journey to net zero.
Matt Colgan, director of Sustainabuild Scotland, said: “Despite many innovative solutions available to help address the impact of embodied carbon, it is clear that without government regulation, support and financial backing, industry-wide adoption will prove challenging, and the industry will not stand a chance in achieving its net zero targets by 2045.”
The newly launched sustainable event at Edinburgh Park hosted key industry speakers who shared their sustainable building innovations – all of which they said have the potential to significantly reduce carbon emissions of building development.
The three speakers raised the same issue around the desperate need to reduce embodied carbon in the delivery of any building project – which can account for up to 75% of a building’s lifetime greenhouse gas emissions.
The Scottish Government recently announced that from January 2025 all new build homes will have to meet a new Scottish version of the Passivhaus standard, meaning they will be expected to be highly energy efficient and well-ventilated.
However, at the event, industry leaders agreed more needed to be done to tackle the climate crisis, calling for tougher regulations around the amount of embodied carbon created to build these new ‘Passivhaus standard’ homes.
Lucy Black, head of business development at Kenoteq, which produce the K-briq, a low carbon, sustainable brick made from almost 100% recycled content, said: “Unlike operational carbon, embodied carbon is not currently regulated, so a project could be declared sustainable in operational carbon terms but be built from the most unsustainably sourced materials.
“Even a Passivhaus could be made using carbon heavy concrete. Innovative embodied carbon saving solutions are plentiful but because of higher costs and lack of regulation, we are likely going to fall very short of our net zero targets.”
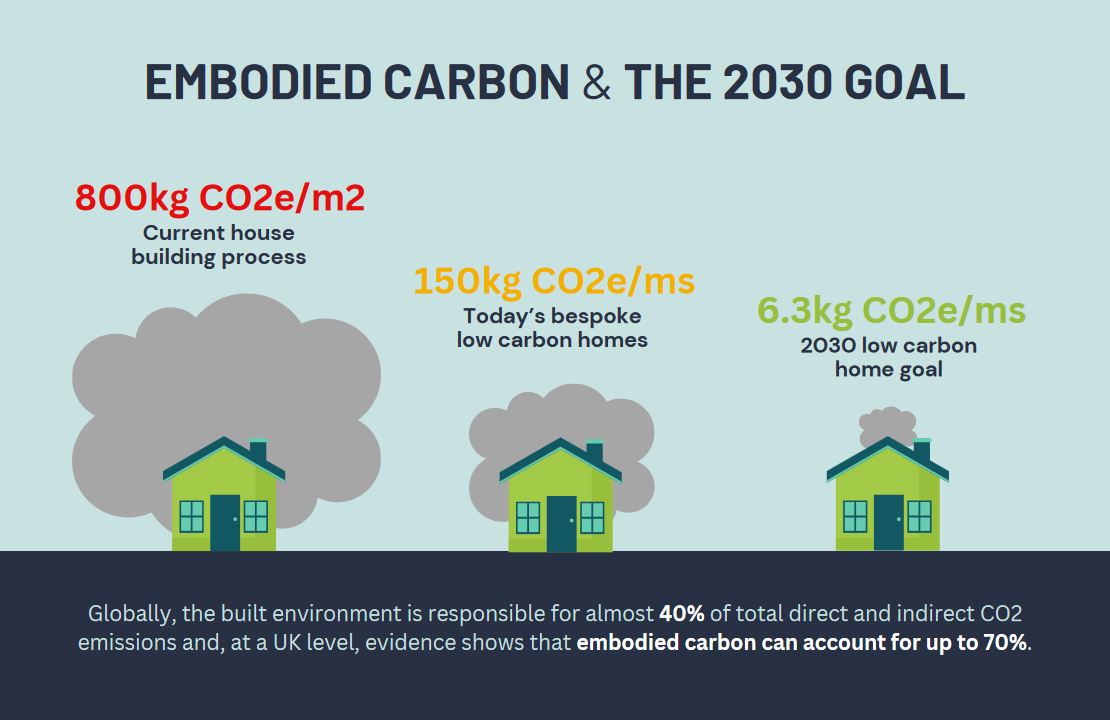
Mike Stevenson, senior manager of strategic markets for NorDan UK, which produces energy-saving low carbon windows, said: “It’s essential that as an industry we think about the whole life cost of any building product. We produce quality windows which are designed to last beyond 60 years.
“Sadly, there are some who will opt for a far inferior quality of product, purely down to its lower initial capital cost, while having no sustainable benefits and will need to be replaced up to three times in the same period. The industry is repeating the same actions and expecting a different result – quite literally the definition of insanity. We must take action now for the future, prioritising eco-friendly and whole life solutions to minimise climate impact.”
Sam Baumber co-founder and chief operating officer of IndiNature, which makes high quality natural fibre insulations, said: “Europe is way ahead of us on the production and use of bio-based materials in construction including industrial hemp which is a wonderfully sustainable material used for insulation as part of the building process.
“This plant literally sucks up carbon as it grows each year – helping create products that capture and store carbon in buildings. Here in the UK, it is now an exciting time - there has been investment of millions of pounds to establish production and first certification of this carbon negative technical insulation and other products, which has unlocked the ability of retrofit and new build projects to use natural fibre insulation at scale.
“The challenge is that without more regulation around embodied carbon in construction, or finance models to support slightly higher upfront cost in these early stages, these products may be overlooked, and cheaper and less sustainable products may just keep on being opted for, missing the opportunity we have now for change at scale.”
Sustainabuild Scotland Breakfast Club is a monthly event designed for professionals focused on driving sustainability in Scotland’s built environment and construction sector. Each month features a different theme with expert speakers.
The next event is Thursday 28th March, with the topic ‘Net Zero Buildings.’
You can sign up for the event here.