Janette Speed: Could COVID-19 be the catalyst for industry to embrace modular housing?
Janette Speed outlines why the modular housing model could have greater appeal as the industry adapts during the current pandemic.
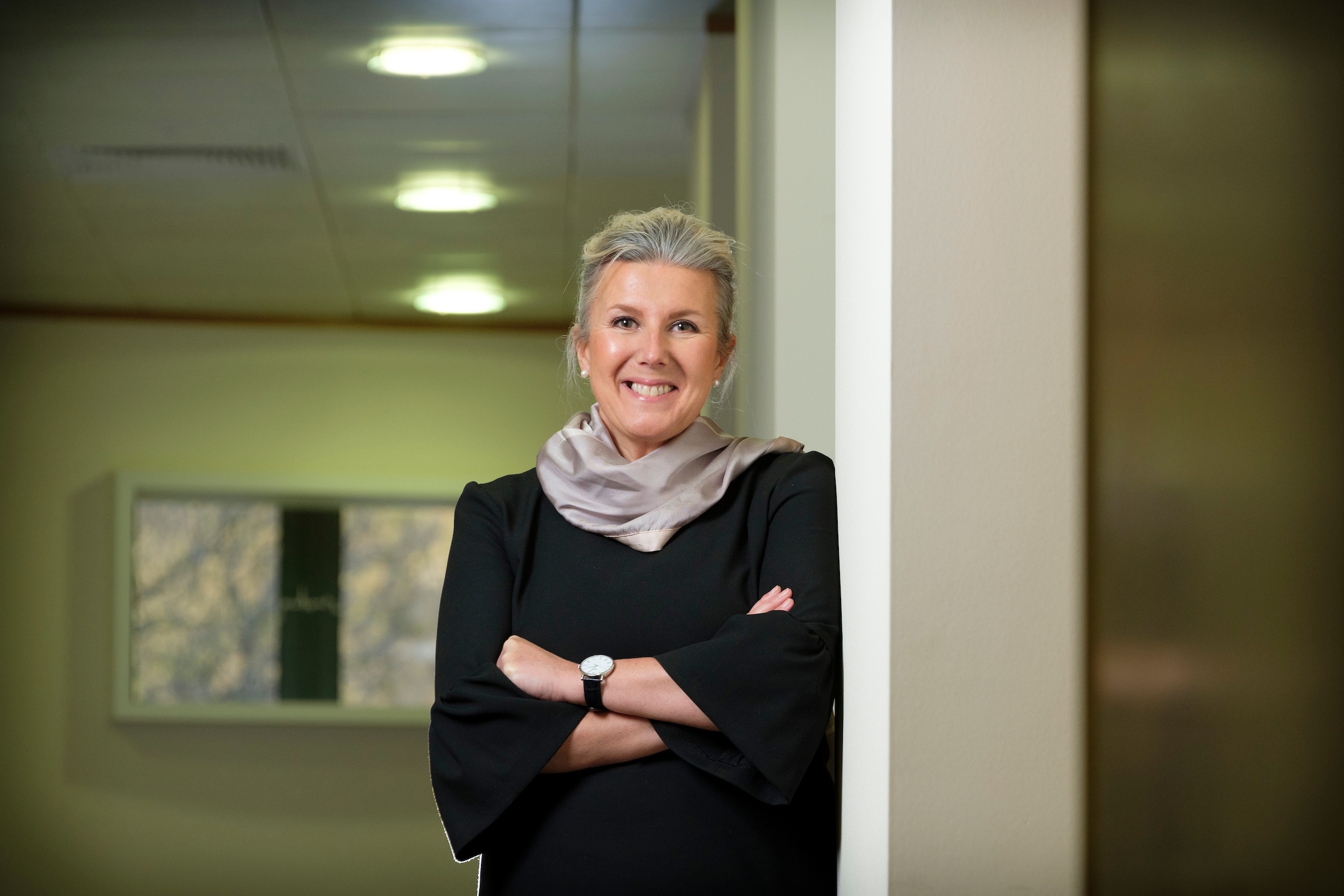
Janette Speed
As the plan to lift the UK out of lockdown is revealed we are all taking a punt at what the new normal is going to look like and how long it is going to take to get there.
The construction sector remains in the eye of the storm and whilst it has been acknowledged for some time that modular housing could allow house building targets to be met due to its potential to deliver homes cheaper and faster, it has struggled to obtain a significant foothold in the UK housing market. Why is this and could COVID-19 be the catalyst for a step change in the industry?
While the benefits of modular housing are hard to ignore, the market has certainly made its views known over the years. The perception remains among buyers that modular housing is similar to post-war homes built in the 1940’s, plagued with the reputation of low quality and inflexibility. This undoubtedly continues to present a challenge and reduces the appetite amongst house-builders to embrace this construction method. In addition, it has to be accepted that buyers and builders alike often have reservations around uniform buildings. This difficulty to influence the design once construction is underway needs to be addressed.
Countries such as Sweden and Japan put modular housing front and centre of their construction industry, but the UK continues to resist the uptake based on issues of scale and quality control. However, in the wake of COVID-19, during which the world witnessed an entire hospital being built in a matter of days, arguably there has never been a better demonstration of the key benefits of offsite construction and its potential to disrupt the methods of the traditional house-building sector.
It is not however a straight forward ‘either /or’ in this post-COVID guessing game. Aside from established financial modelling, structural/delivery and planning complexities alongside political and City imperatives, the demand for housing is ever present. It is entirely understandable that traditional house builders in the UK have resisted these more innovative methods of construction, producing homes at the same rate in which they are sold in order to protect profit margins.
In addition, the investment required to construct the off-site construction factory is significant and one that may not be possible for all house builders. Suitable industrial sites with the necessary infrastructure and links to markets are going to be required. And as with every mass-produced product there remains a question of scale and an upfront risk of an error being replicated throughout production. This along with the long-term investment required for set up improvement and on each modular build itself is something that continues to spook house builders who with few exceptions instead focus on tried and tested methods of delivering homes.
Could it be that the new world might be a place where these approaches may need to work in tandem? Given the challenges faced by the sector in terms of complete shutdown of construction sites across the UK, might house-builders look to invest in the long term and spread the risk in the short to medium term. If there was a fall back option of offsite manufacturing, supply could be preserved, increased or reduced in accordance with demand. The logistics of turning the tap back on may not be as fraught as working out how to get back on site with a range of different contractors, health and safety regulations and potential litigation with the sub-contractors.
In addition, the factory environment of off-site construction may not only increase efficiency but it is also arguably a more appealing environment to the millennial workforce. Academics estimated in 2016 that within 10 years a decline of approximately 25% in the workforce was expected.
Reflecting this research on social homes for rent in Scotland, found that 60% of council officers believed that the skills shortage was one of the main barriers to local authorities building houses in their area. It may be that by incorporating an off-site construction limb, the industry will show itself even more capable of creativity, innovation and adaptability. In essence, a sector that is increasingly nimble and able to react to the challenges presented by the current situation, but also those undoubtedly coming down the tracks. Affordable housing for key workers seems like a prime example of how this model could work.
The impact of COVID-19 crisis in the UK may also reinforce industry focus on the requirement for lower carbon emissions; given the positive impact on the global environment of lockdown, the focus on the carbon footprint of companies will be greater than ever. Alternative construction methods can have a large part to play in this new future. Fewer deliveries are required with modular housing and this will not only reduce carbon emissions, it will also reduce noise pollution at the location of the build.
Alongside fewer personnel and machinery on site, this combines to minimise disruption to the surrounding communities. Whatever the new norm, maybe it is likely to place even more importance on both community and the environment in the planning phase.
The need to appeal to today and tomorrow’s workforce is also key for the housing industry, where an ageing workforce is also an issue. As a senior manager in my own business I know that prospective employees are now more than ever looking for certainty. This is already challenging in traditional construction with high numbers of self-employed contractors and as the skills shortage continues there is surely an argument that the option of off-site construction is an attractive one for both employers and employees alike. Employment opportunities for millennials are going to be key for economic recovery across all sectors.
As a sign of growing momentum in the sector, Legal & General Modular Homes recently re-opened their modular factory. Notably, L&G’s traditional construction operations remain paused (at the time of writing) but with social distancing likely to last beyond lockdown, off-site construction may be more important than ever as a future back up plan.
As Scotland’s target of delivering 50,000 affordable homes by 2021 looks increasingly unlikely, there is a real need for affordable homes to be built quickly, safely and cost-effectively. Offsite construction may not be the silver bullet out of this crisis and the challenges of logistics, scale and government level investment remain in play. However, it is perhaps time that the sector looked at this option more favourably as a complementary solution to delivery of housing in line with the social and political imperative across the UK.
- Janette Speed is head of real estate for Shoosmiths in Scotland