Jo Gilroy: Balfour Beatty goes all electric on Edinburgh Biomes project
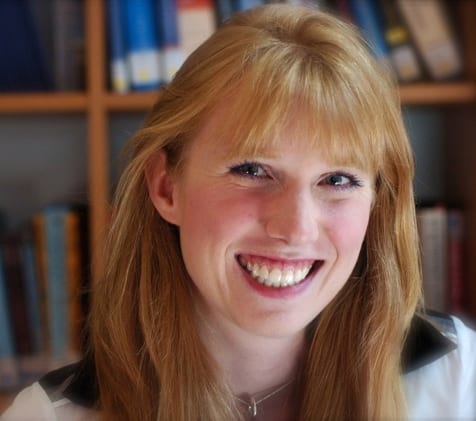
Jo Gilroy
Jo Gilroy, group sustainability director at Balfour Beatty, shares an update on the company’s ongoing journey towards the Zero Carbon Construction Site of the future at the Royal Botanic Gardens Edinburgh.
About this development:
- Authority:Edinburgh City
- Type:Leisure
- Applications:
- Team:Smith Scott Mullan Associates (architect), Nicoll Russell Studios (architect (new public glasshouse) ), Arcadis (project manager/cost consultant ), Harley Haddow (civil and structural engineer/mechanical and electrical services engineer ), Ironside Farrar (landscape architect/planning and consultation )
We have some exciting news to share. For the first time on a live Balfour Beatty site, we’ve gone all electric.
For a duration of six weeks, our team working to deliver our Edinburgh Biomes project at the Royal Botanic Gardens Edinburgh recently trialled a fleet of all electric plant, pushing the boundaries of what is possible and familiarising ourselves with the next generation of telehandlers, excavators, dumpers and wackers.
One of the key challenges that we have faced revolves around electric vehicle charging infrastructure and availability of viable charging stations.
As you can imagine, most battery-powered plant is considerably smaller than diesel plant and therefore only offers enough power for around four-to-six hours of work before it needs recharging.
In addition, as with electric cars and vans, electric plant is far more expensive to hire or purchase than traditional diesel machinery. However, reduced fuel costs and maintenance requirements can make it considerably more cost-effective in the long run. We must also consider that upfront costs are only going to reduce as the industry climbs aboard the electric bandwagon!
There is no doubt that the switch to electric will require changes to the way in which we plan and manage our sites on a day-to-day basis. We’ll need to take action and ensure that we’re charging our electric plant overnight and utilising our Power Profiler tool - which recommends the most cost and carbon efficient site compound set up, wherever possible.
So undoubtedly, there are compromises and hurdles to overcome. However, clearly, one of the main advantages of electric over diesel plant is that they produce zero emissions. This is not only a clear step in the right direction for the construction sector, but it also means that they can operate in enclosed spaces or on smaller sites without additional ventilation and carbon monoxide monitoring.
We have also noticed a clear difference in terms of air quality, and noise pollution too. In fact, the machinery is so quiet during standard operations, our operating procedures and safety training will need to be updated to keep our workforce safe!
However, in spite of all these benefits, all-electric plant isn’t yet a realistic option for our bigger sites, or for heavy plant. The required infrastructure does not currently exist to accommodate a fully electric fleet on a large scale, without a mains grid connection.
That’s why our view is that, for heavy plant, the priority for the industry has to be to accelerate the energy transition to hydrogen rather than rely on electric providing the solution. We are leading the way in making combustion engines work with hydrogen fuel for medium-sized plant such as telehandlers and traditional diggers, through our partnership with JCB and Sunbelt Rentals.
We are also working with GeoPura and Siemens Energy on hydrogen fuel cells to generate power without an electrical connection.
The potential of this work is huge. Replacing diesel generators with hydrogen would see a significant reduction to our carbon footprint, given that 46% of our sites sampled use diesel generators to power temporary accommodation units on site.
Decarbonising the plant used on construction sites is an area that is moving quickly. The giant leap of faith we have just taken at the Zero Carbon Construction Site is one that has been challenging but more than worthwhile. Using smaller and medium sized electric plant is definitely something we will continue to pursue, utilising a mix-and-match approach to help determine the best possible solutions for the future.