Kathryn Sykes: How to approach embodied carbon reduction within home extensions
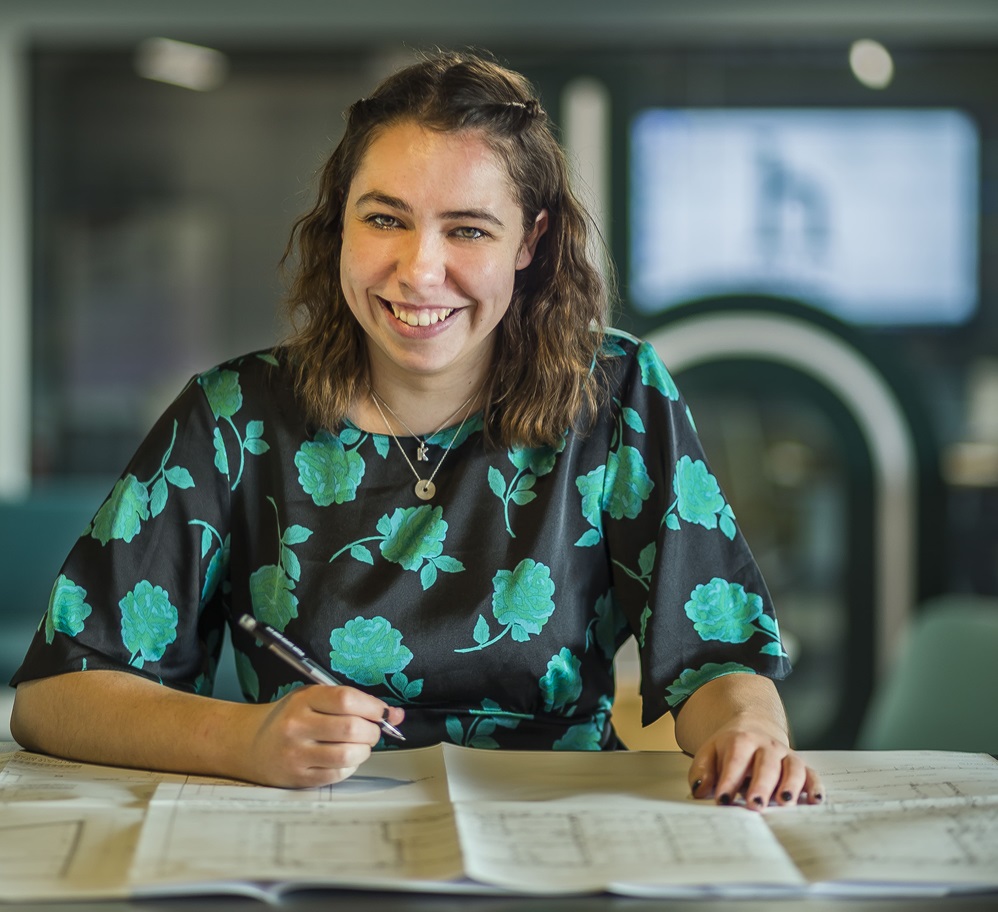
Kathryn Sykes
Kathryn Sykes, structural project engineer at Harley Haddow, argues that it is important to identify how we combat the effects we are having on the environment when making improvements to our homes.
As demand for house extensions continue, is building sustainably the everyday person’s first thought? With 82% of UK adults recognising their role to reduce their own impact on climate change, you could say as a society we are turning a corner. However, when it comes to building a new extension, many may not know where or how to start, both within and outwith the engineering industry.
Many may say that there is no need to discuss sustainability on such a small scale. However, the construction industry is responsible for approximately 40% of global CO2 emissions which therefore means we must be doing everything we can to improve practices. By implementing small changes in the design for house extensions, this can reduce the embodied carbon cost and help reduce our overall emissions.
In Scotland the majority of house extensions are built from timber kit construction, making them inherently more sustainable than their English counterparts. The common material used in England’s construction industry for projects of this size is masonry, which is made up of bricks and blocks.
As someone who works in the engineering industry, I would expect to see an increase in timber kit construction in England going forward as sustainable construction becomes vital. However, at present there is a reservation to adopt timber kit. As an industry we are very reluctant to change and prefer to stay away from the unknown and use tried and tested methods and materials.
The assumption with timber is that it is less robust and more susceptible to fire and water damage. Whilst this is not entirely incorrect, it is not the full picture. As proven by decades of timber kit construction in Scotland and other parts of the world, timber houses can be just as robust and can last just as long as masonry buildings. These buildings can be sufficiently protected from fire and water if designed and installed by those who understand the material and the detailing. For example, Horyuji in Japan is the world’s oldest surviving timber structure having been constructed in 607 AD.
There are many small ways to make an extension more carbon efficient including utilising timber as much as is possible and reducing the quantities of carbon intensive materials such as steel and concrete. For example, changes like adopting a suspended timber floor in place of a concrete slab can help slash carbon emissions.
Already many people are considering the operational energy of their home and making adjustments when they add a new extension. This includes adding PV panels, installing ground or air source heat pumps (with new associated pipework and radiators), improving the insulation in existing walls, floors and roofs. All of these are valuable steps to reducing the overall carbon cost. However, this only addresses the operational carbon which accounts for less than 43% of the carbon in the building. The majority of the carbon is in the building materials and any reduction in these materials is likely to have a much greater effect on the carbon cost than changes to the heating system.
My advice to those considering a house extension is to think it through thoroughly and ensure you have the right team available to you which will help you along the way. There is a perception that sustainable materials are more expensive and in some cases that is correct. However, at Harley Haddow, when we approach any project we try to minimise the material usage where possible so that it is cheaper and also creates less waste. If you lead with minimising the use of material, you can reduce the cost and the carbon.
Here are my top tips when approaching a sustainable housing extension:
- Make sure you have the right people in the room to advise from the start. Having the knowledge and expertise when it comes to a new extension is crucial and can help with project understanding. In some cases, people avoid the unknown as they feel they aren’t an expert but bringing in those who are qualified can help not only the project succeed but also help with understanding.
- Minimise the use of steel and concrete as much as you can. This will really help reduce those carbon emissions in the first stage of constructing the housing extension. We don’t have to eliminate steel and concrete completely as in some cases they are necessary but minimising the use can have an extremely positive affect.
- Understand the brief from the client and what is needed in terms of optimising the existing lay out. For example, large glazed openings (such as bi-fold or sliding doors) often require steel framing around them. Using smaller patio doors, for example, may allow the engineer to design out this steel or reduce it saving cost and carbon while also still giving the client a full height glazed door.
- Calculate the approximate embodied carbon at the beginning of the project. At the scheme design stage, it is very useful for the structural engineer to calculate a rough value for the embodied carbon for the structural elements. This gives a context and is a relatively simple process. It also then allows all parties to clearly understand the carbon impact of design decisions as the project develops.
- Remember your small carbon savings are important. In the last financial year, the structural team at Harley Haddow, in the Edinburgh office alone, has designed just over 100 house extensions. If we could make even a 10% carbon saving across all of those projects, imagine how much carbon we could save every year. We have to start somewhere and we have to start now as this is now a climate emergency.
As an industry that can be reluctant to change, I feel it is essential that we take sustainable changes seriously and stop the assumption that others in the industry will solve the problem. As engineers, we all have a responsibility to drive this to the forefront. Sustainability can seem like a foreign language for new and experienced engineers alike.
However, the resource is out there, speak to fellow engineers, utilise expertise within or outwith your teams, look at upskilling, there are many ways to increase awareness. And it is important to remember that we’re in this together. Housing and house extensions will always be in demand, so if we can make small changes now, hopefully we can see a big change in the future.