New report builds foundations to cut construction’s carbon footprint
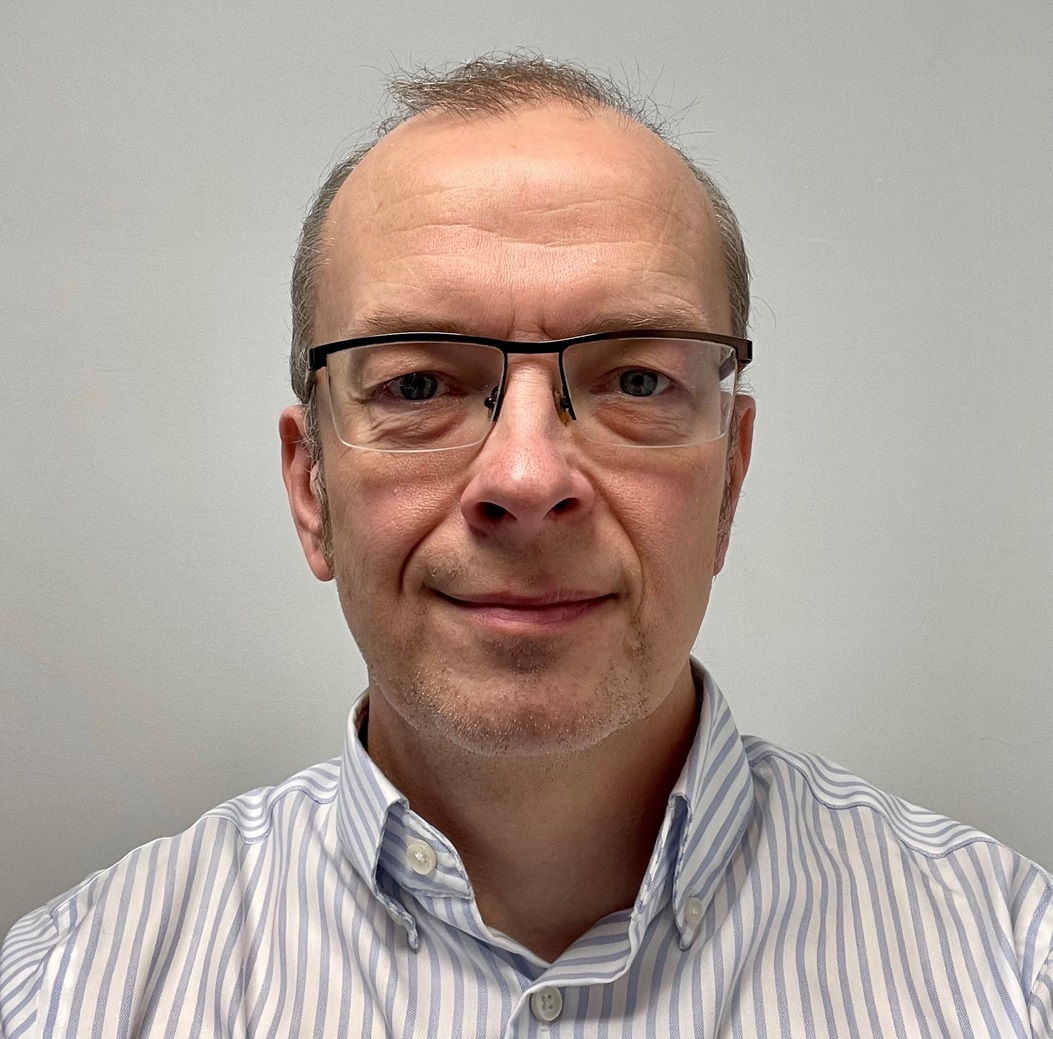
Dr Moray Newlands
Using waste clay and brick in concrete production could significantly reduce the carbon footprint of the UK construction industry, a major new report has concluded.
University of Dundee experts, led by the Mineral Products Association (MPA) with funding from Innovate UK, has demonstrated that UK reclaimed clays and finely ground brick powder can be used as calcined clays in cement and concrete manufacturing to deliver lower emissions compared to the market-leading CEM I cement.
The research found that using waste clay and brick in cement production could reduce the material’s embodied carbon by up to 30%.
The findings also confirmed that calcined clays from these sources have the potential to divert 1.4 million tonnes of material from potential waste streams if the materials were adopted by the UK construction industry.
Experts from the University’s Concrete Technology Unit, based within its School of Science and Engineering, are widely recognised as leaders in the testing of construction materials. For this project, they studied the long-term durability of calcined clay concretes, including suitability for locations near or even in the sea.
“Supporting the UK construction industry to build on the steps it is taking to become more sustainable and help achieve the Government’s legally binding net zero targets is a key priority,” said Dr Moray Newlands.
“Calcined clay is a material that has the potential to make a significant contribution to cutting emissions.
“Our work showed that this material is a viable alternative cement which can be used to supplement Portland cement and provide long-lasting, durable low carbon concrete for many applications including bridges, coastal structures and offshore renewable infrastructure.
“The outputs from this project will also help to develop a stable supply chain for calcined clay within the UK, ensuring the construction industry can have confidence in specifying this material.”
Clay is a naturally abundant material in the UK and can offer an alternative to industrial by-products such as ground granulated blast-furnace slag (GGBS) and fly-ash which have been traditionally used to lower the embodied carbon of cement. UK production of both materials is reducing as the power and steel industries decarbonise.
In other parts of the world, calcined clays are used as a secondary cementitious material but until now they have not been officially tested in the UK.
Two heating methods were trialled to prepare the clay for use in cement and concrete: commonly used rotary kilns, and the more innovative ‘flash heating’. Both methods have been shown to produce high-quality calcined clays, and with no significant difference between techniques.
The project has been supported by Heidelberg Materials UK, Tarmac, Imerys Materials, Forterra, University College London, as well as the University of Dundee.
Dr Diana Casey, executive director, energy and climate change at the MPA, said: “Using brick waste and reclaimed clays will not only lower carbon and reduce waste but has the potential to create a whole new market if these clays become widely used in the construction industry, helping to retain economic value in the UK, secure jobs and attract investment.”
The development of low carbon cements and concretes represent one of seven key levers in MPA UK Concrete’s Roadmap to Beyond Net Zero. The roadmap sets out the UK concrete and cement industry’s commitments to delivering net zero and builds on its decarbonising the industry by 53% since 1990.
You can read more about Dr Newland’s research here.