Stacey Cassidy: Development of modular a key step on the road towards sustainable housing
Stacey Cassidy on modular housing in Scotland and its role in creating a more sustainable housing sector.
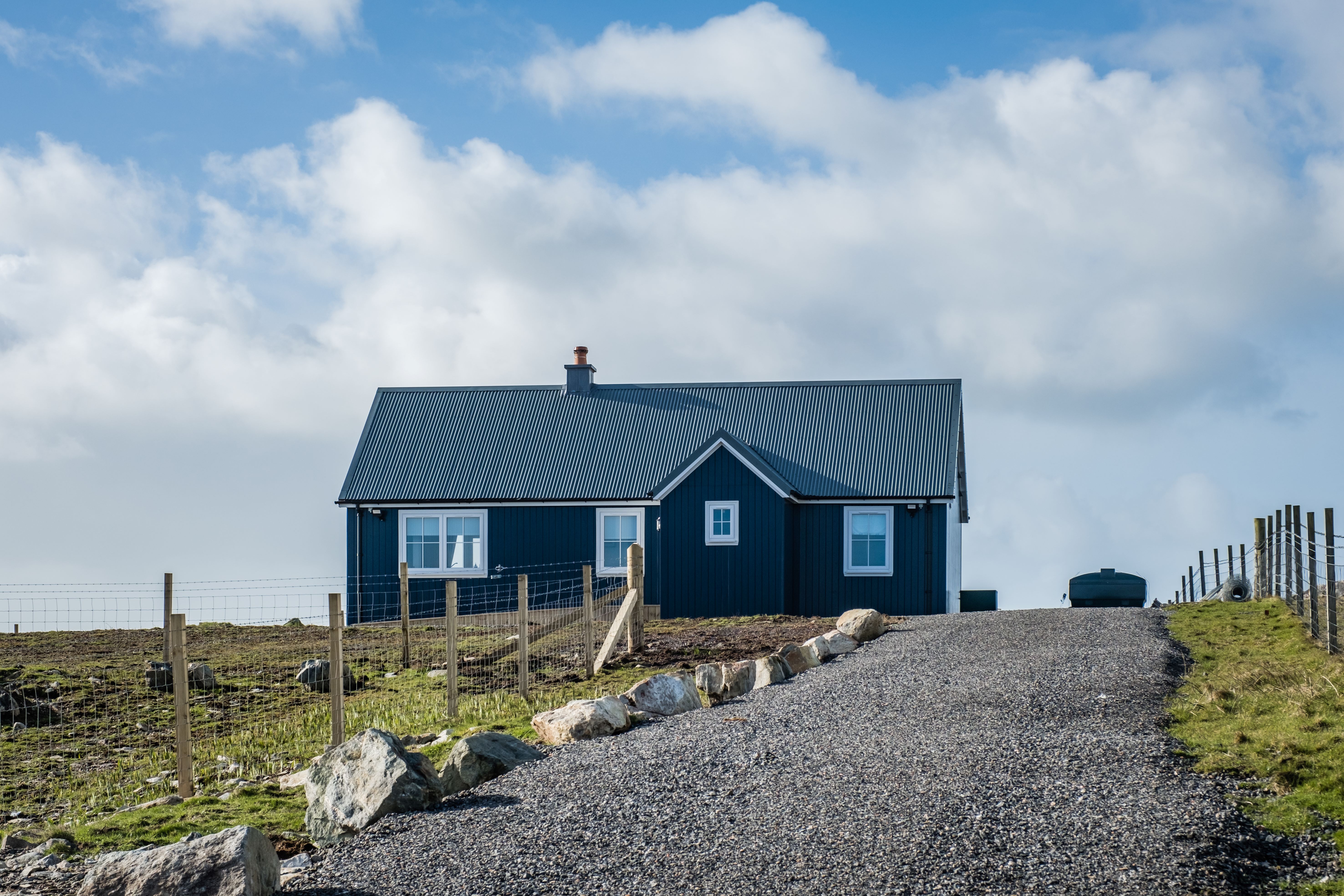
According to the UK Green Building Council, the built environment weighs heavily on the UK’s carbon emissions, contributing up to 40% of our carbon footprint. Given the imperative to reach net-zero carbon emissions in Scotland by 2045 to tackle climate change, the property sector will need to play its part. Whilst this challenge looms large, the growth of modular and offsite manufacturing can provide a solution to the housing sector’s environmental impact, helping to create a more sustainable economy.
There are three main ways in which modular housing can contribute to this – through offsite manufacturing, by developing energy efficient homes and by ensuring a better use of raw materials.
Concentrating fabrication in offsite facilities provides key advantages, notably the opportunity to use clean energy for most of the construction process by ensuring factories are powered by renewables. Such industrial facilities are ideal for the co-location of clean infrastructure (such as wind turbines, solar PV), reducing reliance on carbonised energy sources to power development.
Offsite construction also helps create economies of scale and fosters the development of more efficient local supply chains, both of which can reduce carbon emissions. Indeed, a report published last year by the Construction Scotland Innovation Centre revealed 15 of the largest manufacturing companies operating in Scotland reported that 85% of the products sourced came from suppliers within Scotland.
The decrease in transportation brought about by bringing building for numerous developments under one roof can also minimise traffic and pollution, while retaining a skilled, factory labour force raises productivity levels to help diminish both financial and environmental costs. The study found that offsite manufacturing can reduce the embodied emissions of building materials by 86%, that of the transportation of building materials by 18% and the resource consumption of equipment and techniques by 10%.
Modular can therefore impact on the sector’s fossil fuel emissions during housebuilding but it can equally do so during the property’s lifecycle. Indeed, one of the core benefits of modular housing is that large volumes of homes can be designed with energy efficiency at their heart from the outset. Modern materials can be used en-masse to create highly energy efficient units that reduce heat loss and energy wastage, in turn cutting energy consumption and bills for occupiers.
To take this further, modular homes could even be designed to be carbon neutral from inception, powered by solar panels. These sustainable homes already exist in traditional housebuilding but the efficiencies enabled by offsite manufacturing offer the possibility of such homes becoming far more widespread at an affordable price.
Another important environmental advantage of modular housing is greater efficiency in the use of raw materials. Not only can offsite manufacturing allow for centralised resourcing to ensure the use of sustainably sourced materials at a large scale, but it has been shown to enhance recycling rates during housebuilding, cutting waste and carbon emissions (as fewer raw materials need to be brought in).
Developing homes made of units that are easier to assemble and deconstruct also means that widespread recycling of materials will be possible upon dis-assembly. Indeed, the Construction Scotland Innovation Centre report found modular construction to be more resource-efficient, with 86% of waste materials recycled compared to 75% in traditional construction. Given how the industry accounts for approximately 50% of all waste in Scotland, this recycling uptick would greatly contribute to Holyrood’s Circular Economy Strategy for Scotland.
There is clearly much to be optimistic about but more needs to be done to bring modular housing to maturity. The Scottish Government reports that 80% of new homes in Scotland are already built using offsite construction but most of these only make use of timber frames built offsite rather than wholesale modular units. For modular housing to really take-off, several barriers need to be taken down.
The first of these is the large investment needed to put large modular housing factories into operation and ensure sufficient manufacturing capacity. Another concern is the fact that once these facilities are up and running developers need to pay a large portion of the costs of development upfront to the manufacturer before onsite assembly begins, which can have negative consequences on demand, especially in a risk-averse context. The lack of local skilled labour and local supply chains also provides an obstacle to the rapid acceleration of modular housing.
These challenges are surmountable however and in recent years Scotland has seen numerous modular projects take-off from Edinburgh to the Highlands, notably in the social and affordable housing sector. Businesses and the government now need to come together to formulate an industrial strategy capable of unleashing modular housing.
A national modular housing industry, rooted in local resourcing and distribution networks, can play a key role in making the Scottish housing sector more sustainable – reducing financial costs for businesses and households while minimising housing’s environmental footprint and maximising energy efficiency and quality.
- Stacey Cassidy is a partner at UK law firm TLT