Stewart Dalgarno: We need to make stars align for building zero carbon homes
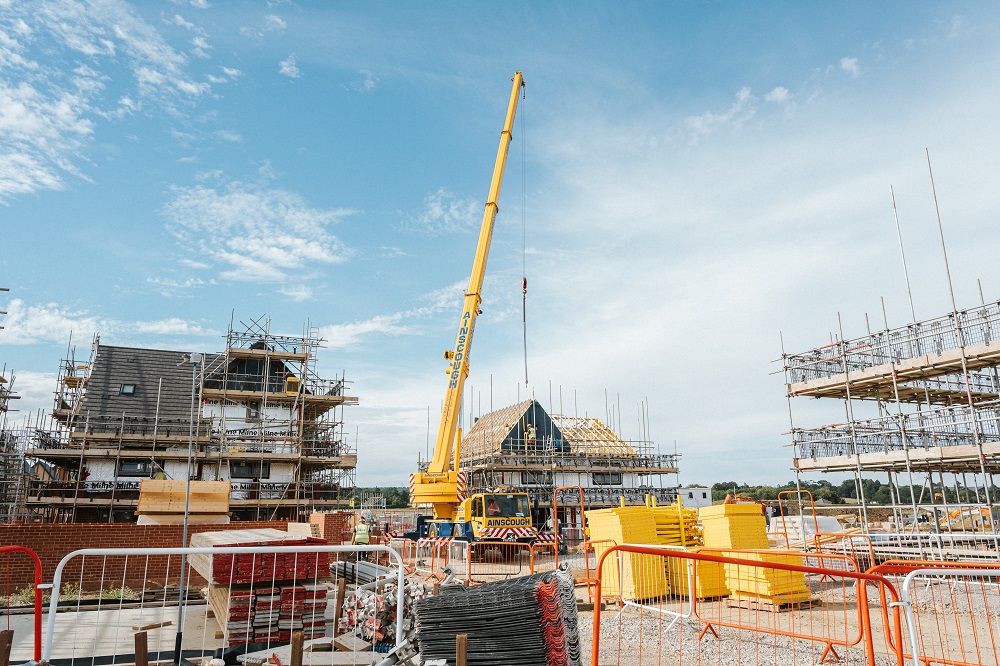
As AIMCH, the UK’s flagship collaborative R&D project, whose aim has been to develop, trial and scale up industrialised housing techniques ends, Stewart Dalgarno, its project director reflects on its achievements and predicts what’s next for the house building sector.
Over the last three years, AIMCH partners have sought to prove the efficacy of adopting near to market, scalable and viable industrialised approaches to housing delivery, such as panelised off-site modern methods of construction (MMC), design standardisation, housing pattern books and advanced manufacturing to build new homes.
This flagship housing innovation programme has been a truly collaborative enterprise involving forward thinking house builders, stakeholders, suppliers, sub-contractors and academia. As it ends, I know that the partners who have been involved, are enormously proud at having helped take their own businesses and the housing sector forward, recognising that housing industrialisation can transform how we build homes, building a strong base, so we can transition towards net zero carbon homes and communities of the future.
Because of our work, scaling up volume production of net zero carbon ready homes in a factory setting, is no longer an abstract concept. Panelised MMC methods and housing industrialisation are here to stay. AIMCH has built the framework, created the rule sets and blueprints for factory investments to scale up production, using automotive expertise and processes to accelerate panelised MMC capacity, as a viable system of choice. As a result, we are going to see very rapid change over the next few years, with huge leaps in housing productivity, output and quality of the homes we build.
Scoring several firsts
Research methods and live site trials have been rigorous. We have tested and compared MMC timber panelised materials and processes with those of masonry built homes, looking at everything from cost, speed, labour, embodied carbon emissions, and on-site health and safety from every conceivable angle. This has culminated in a range of scalable near to market solutions, with the learnings easily adopted by other housebuilders of all sizes, the supply chain and housing associations.
Of the many deliverables achieved, we have delivered several remarkable industry firsts, among which is the UK’s first zero carbon (NZC) concept home. The Z-House was built by AIMCH partner, Barratt Developments in collaboration with Salford University to meet the Future Homes Standard.
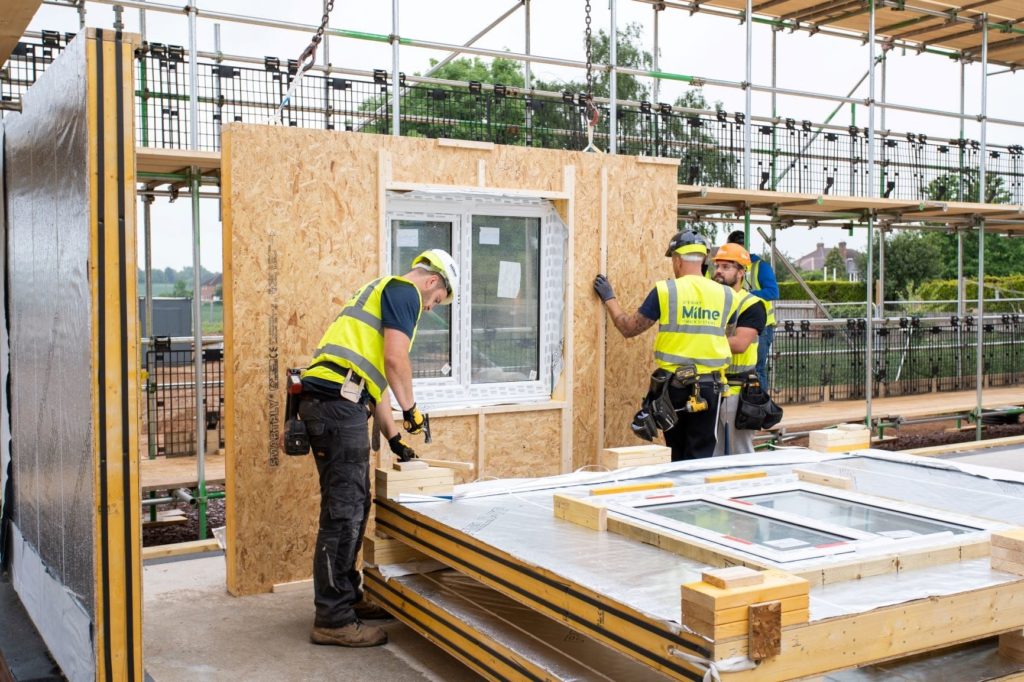
Pattern books of NZC ready affordable homes, which have leveraged learnings from Design for Manufacture and Assembly, Design Standardisation, Product Families and BIM 3D
modelling, have also been produced. These will help SMEs; housing associations and new developers accelerate the speed and volume of new homes being built.
And of note, is the development and investment committed to develop one of the worlds most advanced production lines for open and closed panelised timber MMC build systems, Donaldson Timber Systems (formerly Stewart Milne Timber Systems) using state of art automation and robotics.
More to be done on the MMC agenda
The AIMCH has lived up to its mantra ‘Structural shell built in a day’, ready for cladding and fit out, with the ground being laid for future prefabricated components beyond walls, windows, floor cassettes and roofs to be used, especially in high value areas like bathrooms. These areas are very labour intensive, often accounting for 54% of the work on a new build home. Ripe for the MMC model, as prefabricated bathroom pods, providing a pod and panel building solution of the future, with increased pre-manufactured value (PMV).
However, AIMCH research into standardisation, utilising the L&Q methodology, identified the lack of repetition in bathroom designs, making volume production unattractive and not viable for low rise housing. AIMCH pattern book of homes, are designed to optimise standardised bathroom designs, using a kit of parts, that can provide the platform for future pod and panel hybrid MMC building systems of the future.
The next challenge for the sector is to engage with future MMC pod suppliers to find pathways to greater standardisation and making hybrid MMC systems commercially attractive, using standardised pods and panelised MMC systems, suitable for volume, viable and scalable residential construction.
What of Net Zero Carbon? The biggest challenge lies ahead, life without gas
Net zero carbon homes are absolutely, possible. We know that from the Z-House Concept Home developed by Barratt, as part of AIMCH. The future will be electric and the electrification and integration of homes, communities, and vehicle mobility, with a zero gas decarbonised grid is the next big challenge.
Moving forward, the focus needs to be on assembling a wider collaborative network — house builders, vehicle manufacturers, utilities providers, network operators, energy companies, and the community — to arrive at the most efficient way of scaling what we have learned and plugging AIMCH into an all-electric world.
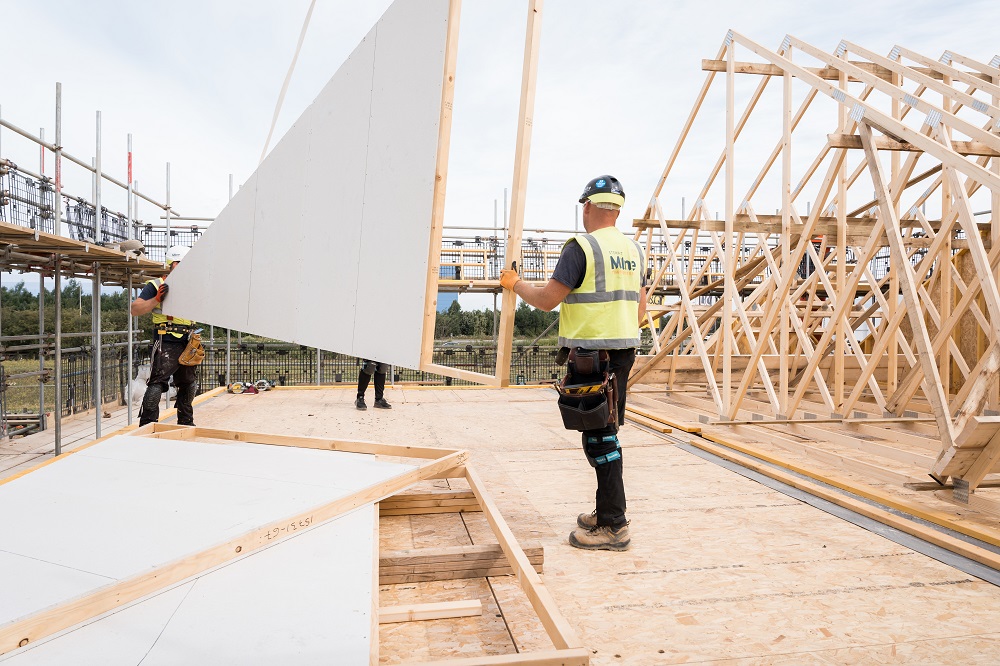
First and foremost, the central objective is for the wholesale electrification of new homes – ditching gas boilers in favour of air pump heating systems, integrated photovoltaic technologies, thermal and power storage and EV charging points. Within 10 years, I would like to see the sector get to the point where all new homes consume only the energy they produce, each home or community acting as its own energy generator, storing power and balancing consumption/generation, so we are at least 50% less dependent on the grid network.
We know that MMC can deliver fabric first solutions to reduce energy demand in perpetuity, the challenge is to plug these into integrated new energy systems at a vehicle, home, or community level, without blowing the network or incurring huge network reinforcement costs, effort, and time that the planet cannot afford.
There is momentum from the sector and from government for working towards that goal. The question which needs to be addressed, however, is whether the grid can be made ready to accommodate the electrification and integration of homes, communities and cars challenge, and what structures need to be in place to allow the deployment of all-electric homes and communities of the future?
On our journey towards net zero carbon, factory-built homes, we do need to be alive to any unintended consequences and we need to continue asking the right questions. For instance: What would a further rise in temperature mean? What might the embodied carbon of a battery look like against the whole life carbon of the home? I suspect that sustainable net zero carbon living will always be a bit of a balancing act.The future energy efficient innovations described in this article do come at a price. However, with ever-increasing energy costs, house buyers will come to see the value of paying upfront for a highly energy efficient home, that can generate, store, and self-consume its own power, with significant off grid reliance. I also predict a shift in market valuation where lenders and surveyors are willing to recognise this value, providing valuations and mortgage rates for these highly desirable future homes.
Housing associations in particular are seeing that paying for better fabric and an energy efficient shell will avoid them costly retrofitting and future tenant disruption to their housing stock in future years as homes require to be upgraded to be net zero carbon in the long term.
AIMCH has demonstrated the path for scaling up industrialised house building using panelised MMC, focused on energy efficient fabric designs, standardisation, digital working, and advanced manufacturing. The next challenge – the electrification and integration of homes, communities, cars, and energy systems, is far greate I hope AIMCH partners can continue to play a central role in transitioning to a life without gas, creating highly valued, all-electric net zero carbon homes and communities of the future.
- Stewart Dalgarno is AIMCH project director and director of innovation & sustainability at Stewart Milne Group